The relentless quest for sustainable and ecologically responsible materials has sparked a keen interest in flax as an alternative to fiberglass in composite manufacturing. This article takes an in-depth look at this transition, highlighting the ecological, economic and structural advantages of flax over fiberglass in various industrial applications.
Technical flax fiber : an overview
Flax (Linum usitatissimum) is an ancient crop whose origins date back millennia in Europe. Used since antiquity for its textile fibers, European flax is today considered a versatile resource for a range of industrial applications.
Technical flax fibers, specifically selected for their strength and durability, are transformed into yarn using state-of-the-art spinning techniques, notably low-twist spinning.
This spinning method produces high-quality flax yarns with enhanced strength and uniform distribution in composites, improving overall material performance.
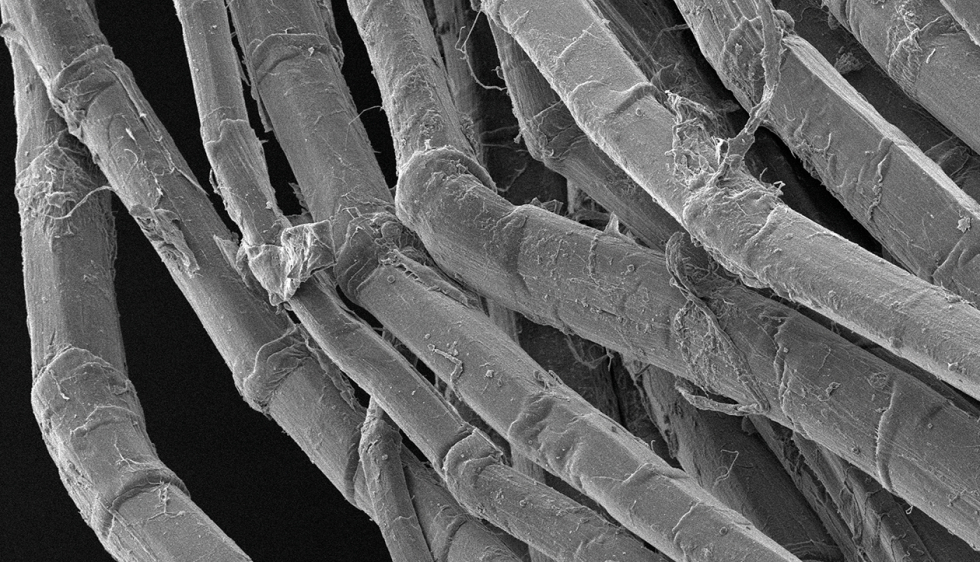
Understanding composites : using linen fiber in composites
Composites are materials composed of two or more components, offering combined properties superior to those of their individual parts. In the case of flax-based composites, technical flax fibers are incorporated into a polymer matrix to form a reinforced structure.
This technique creates a strong, lightweight composite matrix capable of rivaling glass-fibre composites in terms of performance and durability.
A concrete example of the use of flax-based composites in everyday life is the manufacture of automotive parts. Flax-based composites can replace fiberglass in the manufacture of interior and exterior parts such as door panels, dashboards and bumpers.
These composites offer high strength, while being lighter and more environmentally friendly than their fiberglass equivalents. What’s more, they help reduce the automotive industry’s overall carbon footprint.
Advantages of linen fiber as an alternative to fiberglass
Flax fibre is eco-responsible:
Flax is a renewable raw material, grown without excessive use of harsh chemicals. In comparison, the manufacture of fiberglass requires energy-intensive and polluting processes, contributing to the overall carbon footprint. Studies indicate that flax cultivation has a negative net carbon footprint, while fiberglass production is generally associated with carbon dioxide emissions.
The impact of flax production on health :
Emissions of particulates and harmful gases associated with fiberglass production pose potential health risks for workers and the environment. Flax processing, on the other hand, is less toxic and poses less risk to human health.
Reducing the carbon footprint :
Flax, as a low-carbon footprint crop, absorbs carbon dioxide from the atmosphere as it grows. As a result, flax-based composites help reduce the overall impact of industry on climate change.
Support for french industry :
France is the world’s leading producer of linen, making it a local resource for the composites industry. Promoting the use of flax strengthens the local and regional economy, creating opportunities for employment and economic growth.
Fiberglass production in France is also significant, although its environmental impacts and economic implications differ from those of flax production. Statistics on fiberglass production in France indicate a significant annual output, mainly used in sectors such as construction, automotive, and the sports and leisure industry. However, this production can be associated with high environmental costs, particularly in terms of energy use and waste production.
Future challenges and prospects for flax fiber
Although flax offers many advantages over fiberglass, challenges remain. The availability of high-quality technical flax fiber and composite manufacturing processes still require improvement to fully rival glass fiber in terms of performance and cost. However, with the growing emphasis on sustainability and environmental responsibility, flax is becoming increasingly attractive to industries seeking to reduce their environmental impact while remaining competitive in the marketplace.
There are still many applications to be developed in the various industries mentioned below :
Flax fiber in construction and architecture :
Flax-based composites are increasingly used in construction to make building panels, façade elements, flooring and lightweight structures. Their strength, durability and low weight make them attractive materials for architectural projects requiring durable and aesthetic solutions.
Linen in aerospace industry :
Flax-based composites also find applications in the aerospace industry, where their lightness and strength are essential characteristics. They can be used in the manufacture of structural components for aircraft, helicopters and satellites, helping to reduce the overall weight of aerospace vehicles and improve their energy efficiency.
Flax fiber for outdoor sport equipment :
Flax-based composite materials are used in the manufacture of sports equipment such as tennis rackets, golf clubs, surfboards, bicycles and protective gear. Their lightness, strength and shock absorption make them popular choices for professional and amateur athletes alike.
Flax fibre composites in the maritime industry :
Flax-based composites are also used in the marine industry to manufacture boat hulls, masts, decks and navigation equipment. Their corrosion resistance and light weight are valuable features in maritime environments, where durability and performance are essential.
Manufacture of protective and safety equipment:
Flax-based composites are used in the manufacture of personal protective equipment such as helmets, body armor and fall protection equipment. Their ability to absorb shock and provide impact protection makes them valuable materials in many sectors, including construction, industry and emergency services.
We’re not about to see fiberglass disappear from composite materials, and flax could never totally replace it. Nonetheless, there is a place for industries wishing to produce more virtuously. As the saying goes, Rome wasn’t built in a day!
In conclusion, flax is emerging as a viable and promising alternative to fiberglass in composite manufacturing. Its advantages in terms of ecology, health, carbon footprint and support for the local economy make it an attractive choice for industries seeking to reduce their environmental impact while remaining competitive in the marketplace.
With increased investment in research and development, flax has the potential to transform the composites industry, paving the way for a more sustainable and resilient future.