Flax preparation

Combing is followed by a preparatory stage. Similar to a champagne manufacturer, Safilin blends at least 24 batches of combed ribbons originating from different locations and different harvest years in order to make a linen yarn of homogenous quality and colour, regardless of the harvest quality.
Safilin is the only linen spinning factory in the world to have a stock of scutched fibres sufficient for over 10 months of production. This allows us to compensate for the risks related to the harvest quality.
Combed flax fibre ribbons will be mixed in a complex blending process. Preparation is composed of 5 stages; at each stage, the ribbons are mixed and stretched to obtain a sliver. This process may last around a week. At the end of these 5 stages, the sliver will be slightly plied.
Washing and bleaching
Following the preparatory stage, the sliver will be washed and then may be bleached, to prepare it for dyeing. These operations last around 8 hours and allow washing out of the remaining pectin present in the fibre, giving it its sandy colour that we know so well. The sliver will then rest for some time to eliminate the excess of water.
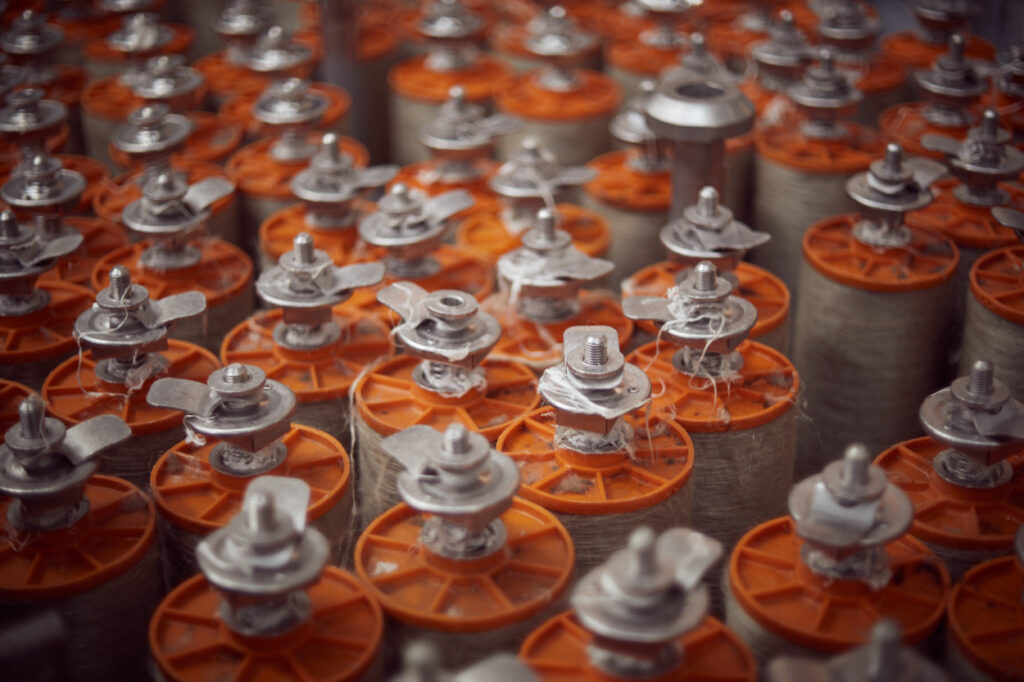
Linen spinning
The sliver will then be added to others waiting to be spun. It will be humidified to achieve the desired finesse, robustness and homogeneity. The last stage will be to ply it to complete the transformation and obtain the linen yarn. We use 2 different spinning technologies:
- dry spinning: using combing (by-product of our combing) or scutching (by-product of our scutching) flax tow that we will card and spin. The final fibre is thicker and more rustic, and it is generally used in the clothing industry.
- Wet spinning: we use solely long, combed fibres. We use them to manufacture thinner and more regular yarn. This yarn is dedicated mainly to the clothing industry, table/bed linen and curtains manufacturing.
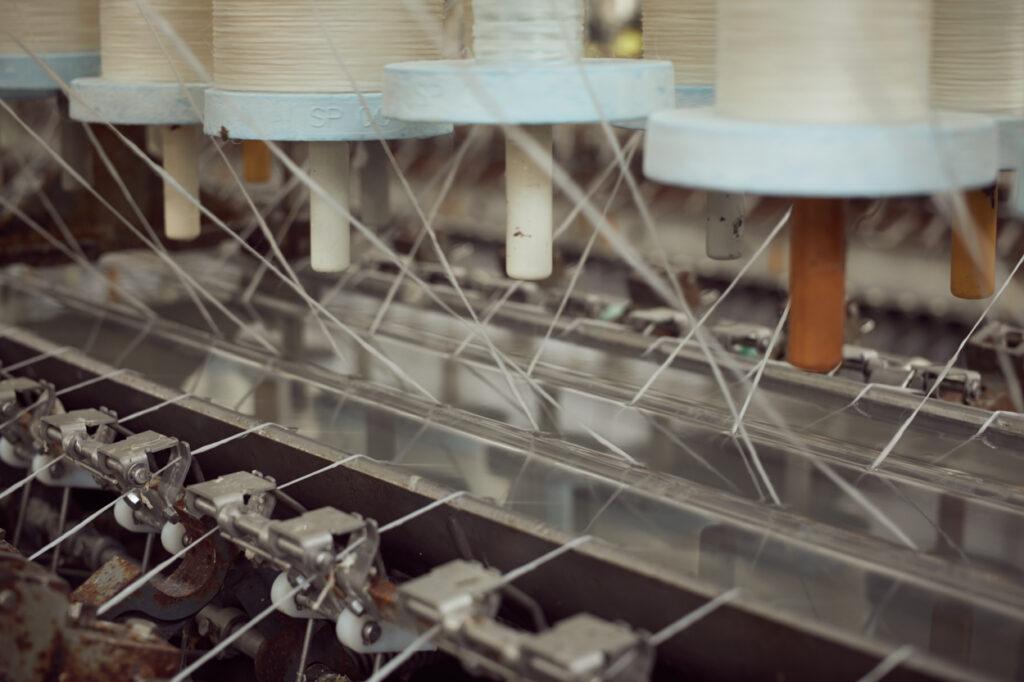
Winding, the last stage of linen spinning
This last stage is where we carry out the final quality control before sending the spools to our customers. Our tools are equipped with the state-of-the-art technologies detecting and removing defects before the final packing.
Weaving cones, packed for dyeing, on cardboard tubes, without tubes, entwined, in balls… our winding workshop answers many different product presentation requirements. The spools are then closed in bags (for those that were wet-spun), to preserve their humidity level, loaded onto pallets and sent to our customers.
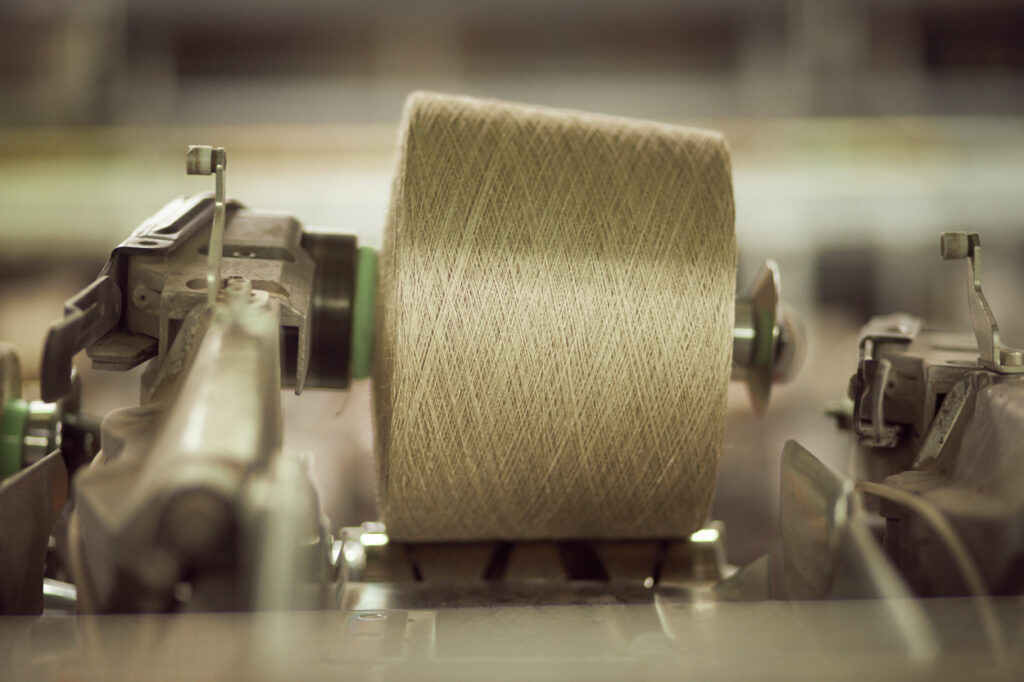
Linen spinning is a complex process requiring qualified and experienced personnel with a perfect mastery of gestures, necessary in this job. It’s an entirely mechanical transformation, requiring know-how and constant monitoring in order to be able to offer a premium quality yarn that will then create a premium quality, lasting product.