From scutching to combing to winding, flax fibre undergoes a number of stages before it becomes the Safilin flax yarn you know.
After being cultivated until the summer After cultivation, flax fibre undergoes several processing stages in order to become flax yarn:
Manufacturing flax yarn : Scutching
Following the retting process, the windrows are pressed into bales and stored. Next comes the scutching stage. Scutching is a mechanical operation that separates the flax fibres from the bark of the plant, which is done by means of grinding and beating.
The long fibres are stored for subsequent combing.
The shives (the bark of the plant) are retrieved and used to make chipboard panels or animal bedding.
The short fibres, known as scutching tow, will serve to make thicker, more rustic yarns, used in particular for manufacturing furniture and twine.
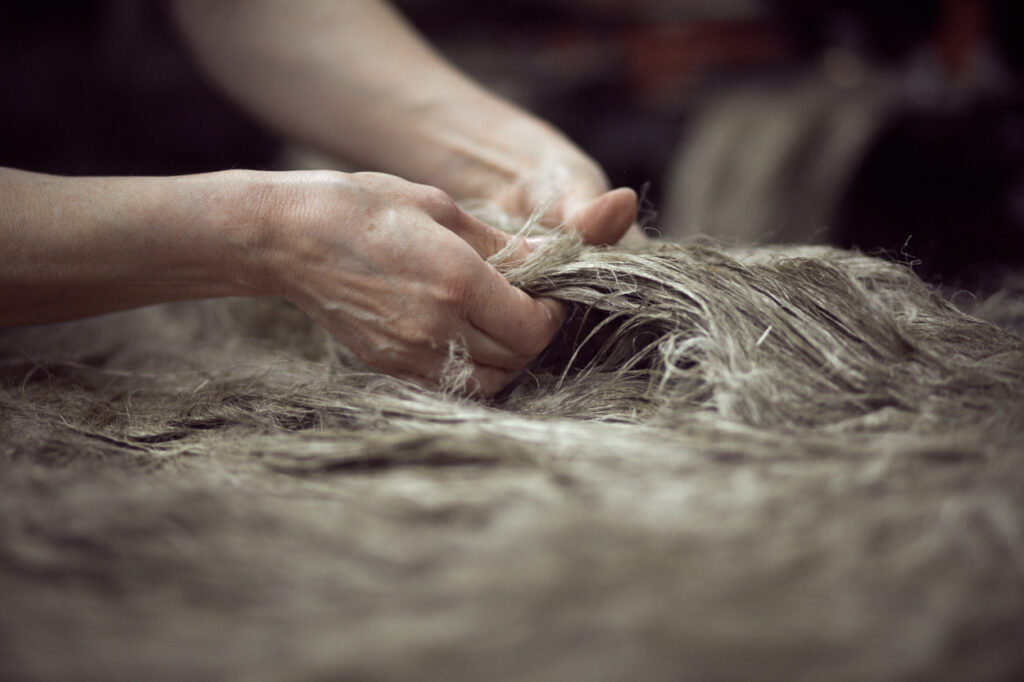
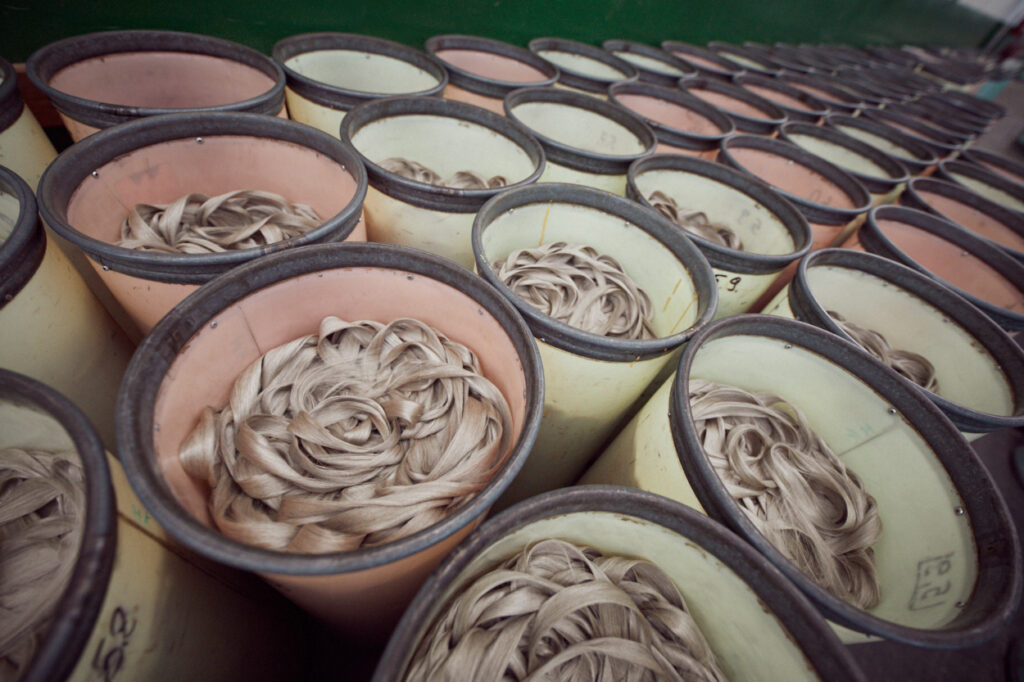
Manufacturing flax yarn : Combing
The long fibres are then combed, which is a crucial stage in the preparation of quality flax yarn. The combing is usually done at the scutching facility. At Safilin, however, we have opted to do our combing in-house, buying the dyed fibre and combing it ourselves.
Combing is carried out with increasingly fine combs. This step is crucial to remove the last tiny pieces of straw. It also helps to gradually separate the fibres from one another.
During the combing process, ribbons of flax fibre are formed. The fibres are bundled together to form a ribbon, stretched to a greater or lesser extent to increase its strength, depending on its future use.
Manufacturing flax yarn : Spinning the flax fibres
Preparation:
The quality of Safilin flax yarn is also owed to the preparation process. No less than 25 combed ribbons from different regions and years are mixed together to create the most homogeneous sliver possible.
For spinning, two very different processes are used:
- Wet spinning: this process serves to obtain top quality flax yarn, often used in the clothing and household linen sector. In this process, the flax sliver is soaked in water of approximately 70°C in order to make it more flexible and thus enable the production of finer yarns.
- Dry spinning: in this case, the linen yarns turn out thicker, with more of a rustic feel to them. This process consists in spinning the linen ribbons without first soaking them in water. These yarns will be used for decorative fabrics or for technical purposes.
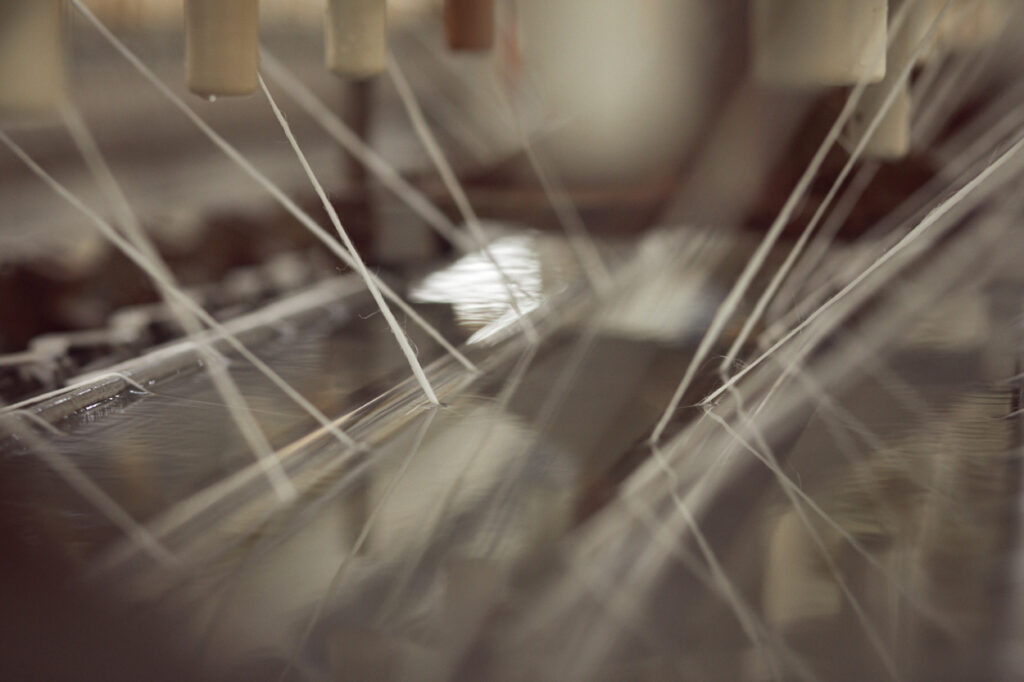
The last step is the winding – cones for weaving, dyeing, cardboard… Our winding workshop can accommodate a variety of presentations to meet your needs.
From now on, when you look at your spool of Safilin flax yarn, you will be able to picture the entire process, from fibre to yarn, carried out entirely in Europe.
Video of the transformation from fibre to yarn: